Seals are used to prevent fluids from passing through a specific point, as well as to prevent air and dirt from entering the system where they are used. The increasing use of hydraulics and pneumatics in aircraft systems has created the need for washers and couplings with different features and designs to cope with the wide range of speed and performance variations to which they are subjected. There is no one-size-fits-all connection or type of connection.
Some reasons for this:
– Pressure at which the system operates
– Type of fluid used in the system
– Metal surfaces and clearances between adjacent parts
– Type of movement (rotational or translational) if any.
Seals are divided into three main categories: Seals (O-rings), Seals and Sealing rings.
Watertight Seals
Seals are made of synthetic or natural rubber, also Viton, Nitrile, or any other material. They are often used as “working seals”, i.e. in assemblies containing moving parts, such as transformers, pumps, multi-way valves, etc. Seals are manufactured in the form of O-rings, V-rings and U-rings, each of which is designed for a specific purpose.

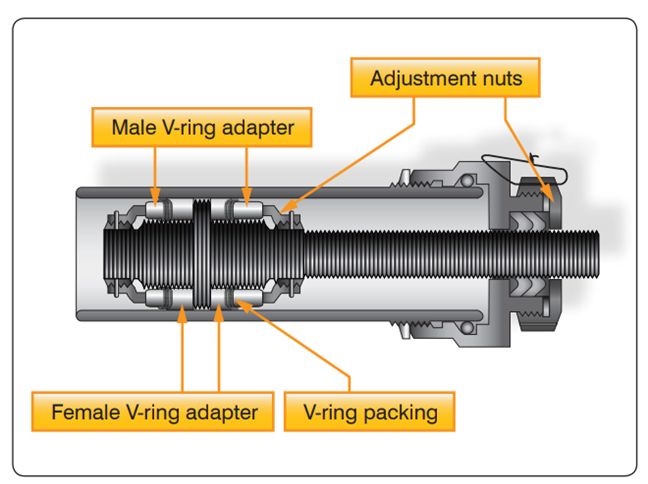
O – RINGS. MS28775-222
O-Rings are used to prevent leakage from both the inside and outside of the element we are trying to make watertight. This type of gasket has an effective seal in both directions and is the most commonly used. In equipment operating at pressures above 1500 psi, back-up rings with O-rings are used to prevent extrusion.
When O-rings are pressurised on both sides, as in transmission cylinders, two spare O-rings (one on each side of the O-ring) should be used. When the O-ring is pressurised on one side only, a backup ring is often used. In this case, the back-up ring is always located on the side of the O-ring away from the pressure.
O-ring materials are designed for a wide range of operating, temperature and fluid conditions. O-rings are specifically designed for use as a static (non-moving) seal that cannot function when installed on a moving part, such as a hydraulic piston. Most O-rings are similar in appearance and construction, but their performance can vary greatly. The O-ring is useless if it is not compatible with the system fluid and operating temperature. Advances in aircraft design required new O-ring formulations to meet new operating conditions. Hydraulic O-rings were originally manufactured to AN specification numbers (6227, 6230, and 6290) for use in MIL-H-5606 fluids from -65°F to 160°F. As new designs have increased the operating temperature to 275°F, many connections have been developed and improved.
Recently a compound has been developed to improve low temperature performance without sacrificing high temperature performance, rendering other product lines obsolete. This superior material was used in the MS28775 series. This series is now the standard for MIL-H-5606 systems where temperatures can range from -65 °F to 275 °F. Manufacturers provide colour coding on some O-rings, but this is not a reliable or complete method of identification. Colour coding systems do not specify dimensions, only the compatibility of liquids or vapours within the system and, in some cases, the manufacturer. MIL-H-5606 liquid compatible O-ring colour codes always include blue, but may also include red or other colours. Seals and washers suitable for use with Skydrol™ fluids always have a green stripe, but may also have blue, grey, red, green or yellow dots as part of the colour code. The colour codes for O-rings compatible with hydrocarbon oils always include red, but never blue. A coloured band around the perimeter indicates that the O-ring is a sealed face. The colour of the O-ring indicates fluid compatibility: red for fuel, blue for hydraulic fluid.
We can manufacture following different colour logics to apply this sealing element to your requirements.
The coding on some rings is not always the same and may vary depending on different aspects. On others it may be cancelled or replaced due to manufacturing/supply difficulties or interference with operation. In addition, the colour coding system does not allow to establish the age of the O-ring and its temperature limits; taking into account the expiry date of the materials for the correct use of the sealing element.
Due to the difficulties of colour coding, we pack the O-rings in individual airtight envelopes with zip closure and labelled with all the relevant data. When selecting an O-ring for installation, the basic part number on the sealed envelope provides the most reliable identification of the compound. We also include the batch number and expiry date as well:
Shelf life of NBR 4 YEARS.
Shelf life of NEOPRENE 4 YEARS.
Shelf life of VITON 10 YEARS.
Shelf life of VMQ (silicone) 10 YEARS.
EPDM shelf life 6 YEARS.
Although an O-Ring may appear to be perfect at first glance, there may be slight surface defects or defects in the material composition for important details such as hardness. These defects are often capable of preventing satisfactory O-ring performance under the varying operating pressures of aircraft systems; therefore, O-rings should be rejected for defects that affect their performance. Such defects are difficult to detect, and one aircraft manufacturer recommends using a 4x magnifying glass with adequate lighting to inspect each O-ring before installation. We work with optical testing, hardness testers and calipers to guarantee a perfect result, and adapted to the corresponding needs.
By rolling the ring over an inspection cone or spigot, the bore surface can also be checked for small cracks, particles of foreign material or other irregularities that cause leakage or shorten the life of the O-ring. The slight stretching of the ring when it is rolled inside out helps to reveal some defects that are not otherwise visible.
O-Ring Military, Military Gasket, Military Washer Flat, Military Retaining Ring, Military Seal.
PNR 1040 MFC F6101 NSN 5330-14-4751269. Material GASKET.
PNR 100713 MFCF6177 NSN 5331-14- 2380551. Material O-RING.
PNR 00925B7800A03V7 MFC F0235 NSN 5331-14- 5443892. Material O-RING.
PNR 01560B7800A03V7 MFC F0235 NSN 5331-14- 5443895. Material O-RING.
PNR 02029C6200A60C7 MFC F0235 NSN 5331-14- 4378654. Material O-RING.
PNR 02035B7800A03V7 MFC F0235 NSN 5331-14- 5443897. Material O-RING.
PNR 02315-0470-0050 MFC 59885 NSN 5310-01- 5244959. Material NUT, SELF-LOCKING, HEXAGON.
PNR 04150C0000A60C7 MFC F0235 NSN 5331-14- 3244644. Material O-RING.
PNR 095-20100 MFC 33269 NSN 5310-01- 5652318. Material WASHER, FLAT.
PNR 095-20900 MFC 33269 NSN 5310-01- 5652321. Material WASHER, FLAT.
PNR 1,8X9,5-64C8 MFC F5442 NSN 5331-14- 4191017. Material O-RING.
PNR 154-07301 MFC 33269 NSN 5330-01- 5816354. Material SEAL, PLAIN ENCASED.
PNR 154-13400 MFC 33269 NSN 5330-01- 6480832. Material SEAL, PLAIN ENCASED.
PNR 155-16800 MFC 33269 NSN 5325-01- 5816360. Material RING, RETAINING.
PNR 2,62X94,92-61D6 MFD F5442 NSN 5331-14- 5602208. Material O-RING.
PNR 2-013C557-70 MFD 7060 NSN 5331-00- 3520327. Material O-RING.
PNR 2-013V747-75 MFD FAQB2 NSN 5331-14- 5562685. Material O-RING.
PNR 2-014 C557-70 MFD 2697 NSN 5331-01- 1359513. Material O-RING.
PNR 2-014V747-75 MFD FAQB2 NSN 5331-14- 5562684. Material O-RING.
PNR 23111AG050L MFD F0111 NSN 5310-14- 2056264. Material WASHER, FLAT.
PNR 23111AG060LE MFD F0111 NSN 5310-14- 3395084. Material WASHER, FLAT.
PNR 23111AG100LE MFD F0111 NSN 5310-14- 3436455. Material WASHER, FLAT
PNR 23111UB080 MFD F0111 NSN 5310-14- 2504991. Material WASHER, FLAT.
PNR 23116AG050LE MFD F0111 NSN 5310-14- 3469188. Material WASHER, FLAT.
PNR 23118AG050LE MFD F0111 NSN 5310-14- 3534506. Material WASHER, FLAT.
PNR 23119CM140E MFD F0111 NSN 5310-14- 5327840. Material WASHER, FLAT.
PNR 23134AG220LE MFD F0111 NSN 5310-14- 4437165. Material WASHER, FLAT.
PNR 23142AG160LE MFD F0111 NSN 5310-14- 4129046. Material WASHER, RECESSED.
PNR 23201AM0180L MFD F0111 NSN 5325-14- 2515867. Material RING, RETAINING.
PNR 23201AM0280T MFD F0111 NSN 5325-14- 3415537 RING, RETAINING.
PNR 254108411E MFD F1989 NSN 5330-14- 5375496 GASKET.
PNR 26.7X1.78-GT40 MFD F4321 NSN 5331-14- 5058308 O-RING.
PNR 261523410-0101 MFD FAQ15 NSN 5998-14- 5787457 CIRCUIT CARD ASSEMBLY.
PNR 29627164-00 MFD FAQ15 NSN 5330-14- 5479346 SEAL, NONMETALLIC SPECIAL SHAPED SECTION.
PNR 2PA108 MFD F0224 NSN 5310-14- 3108005 NUT, SELF-LOCKING, HEXAGON.
PNR 3,53X180-21A7 MFD F5442 NSN 5331-14- 5645477 O-RING.
PNR 3001S747 MFD F6101 NSN 5330-14- 5406126 GASKET.
PNR 3001S823 MFD F6101 NSN 5310-14- 5468069 WASHER, FLAT.
PNR 3-910C557-70 MFD 2697 NSN 5331-01- 0156657 O-RING.
PNR 3X14,2X2-20A7 MFD F0235 NSN 5330-14- 5245231 GASKET.
PNR 46012A00710 MFD F0111 NSN 5331-14- 4677665 O-RING.
PNR 4678918ª MFD F0057 NSN 5330-14- 5392843 GASKET.
PNR 4X15,9X2-20A7 MFD F0235 NSN 5330-14- 5430823 GASKET.
PNR 4X21-64C8 MFD F5442 NSN 5331-14- 5420997 O-RING.
PNR 6-002V747-75 MFD FAQB2 NSN 5331-14- 5559750 O-RING.
PNR 81810-170-50D7 MFD F5442 NSN 5331-14- 3161849 O-RING.
PNR 81810-190-21B6 MFD F5442 NSN 5331-14- 2853801 O-RING.
PNR 8599-5547 MFD F0479 NSN 5330-14- 5517432 GASKET.
PNR 9017A1007-01 MFD D9893 NSN 5330-12- 3749240 GASKET.
PNR 9045F0002-01 MFD D9893 NSN 5331-12- 3659490 O-RING.
PNR 999CA200-15 MFD A2829 NSN 5330-15- 1983297 GASKET.
PNR AN763-12 MFD 88044 NSN 5330-00- 2914714 GASKET.
PNR AS3209-007 MFD 81343 NSN 5331-01- 0332708 O-RING.
PNR AS3209-010 MFD 81343 NSN 5331-00- 0050483 O-RING.
PNR AS3209-011 MFD 81343 NSN 5331-00- 1660975 O-RING.
PNR AS3209-012 MFD 81343 NSN 5331-00- 1660980 O-RING.
PNR AS3209-138 MFD 81343 NSN 5331-00- 5373929 O-RING.
PNR AS3209-167 MFD 81343 NSN 5331-00- 5493628 O-RING.
PNR ASNA0360-05010 MFD F5442 NSN 5310-14- 5391793 WASHER, FLAT.
PNR DIN65202A0112M3 MFD D8286 NSN 5331-12- 3664691 O-RING.
PNR DIN65202A0118F1 MFD D8286 NSN 5331-12- 3629900 O-RING.
PNR EN3746A0100 MFD I9005 NSN 5331-15- 1993691 O-RING.
PNR EN3746B0200 MFD I9005 NSN 5331-15- 1993692 O-RING.
PNR GSC-21-96452-020 MFD C1462 NSN 5330-12- 3618933 GASKET.
J221P012 A3460 5331-15- 1985545 O-RING
J221P021 7482 5331-00- 1661010 O-RING
J221P022 7482 5331-00- 1661011 O-RING
J221P026 7482 5331-00- 1661025 O-RING
J221P110 A3460 5331-15- 1985548 O-RING
J221P906 A3460 5331-15- 1985550 O-RING
J221P912 A3460 5331-15- 1985552 O-RING
J228P011 7482 5331-00- 2470813 O-RING
J228P013 99207 5331-00- 7597069 O-RING
J228P041 7482 5331-01- 0932486 O-RING
J228P110 99207 5331-01- 4435939 O-RING
J228P112 7482 5331-01- 1185698 O-RING
J228P113 66001 5331-00- 8263368 O-RING
J228P226 7482 5331-01- 1149262 O-RING
JSAER/ OP NH-90 J228P238 7482 5331-01- 1469923 O-RING .
PNR MA3352A0095 MFD 81343 NSN 5331-01- 4993523 O-RING
Seals – Sealing gaskets. MS28782 Seals.
Seals (MS28782) made of Teflon™ will not wear out over time, are unaffected by system fluids or vapours and can withstand extreme temperatures, well above those found in a high pressure hydraulic system. Their pitch number not only indicates their size, but is also directly related to the pitch number of the O-ring into which they are fitted. They can be purchased with different but interchangeable key part numbers; this means that any Teflon™ replacement ring can be used to replace any other Teflon™ replacement ring as long as it has the correct overall dimensions to hold the proper O-ring. Shipping rings are not colour coded or otherwise and must be labelled on the packaging.
Inspection of replacement rings shall include examination of surface roughness, clarity and sharpness of edges, and parallelism of chamfered edges. When inspecting Teflon™ spiral retainers, ensure that the threads are not stretched more than 1 ⁄4 inch when not attached.
V-RINGS
The V-type seal (AN6225) is a single-sided seal and is always installed with the open end of the “V” toward the pressure side. V-RINGS must be fitted with a male/female adapter to hold them in place after installation. It is also necessary to tighten the gasket support to the torque specified by the service part manufacturer; otherwise, the gasket may not function properly.
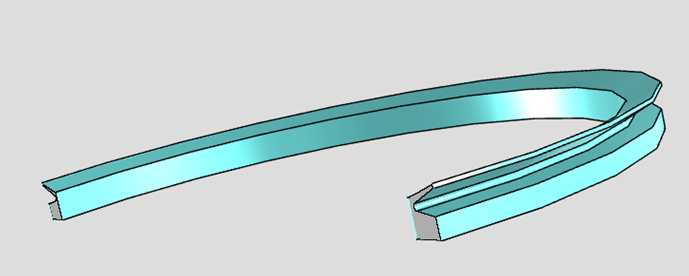
U-RINGS
U-ring seals (AN6226) and U-ring seals are used in the brake and master cylinder assembly. U-Rings and U-Rings are compressed in one direction only; therefore, the seal edges must withstand the pressure. U-Rings are primarily low pressure seals for use below 1000 psi.

GASKETS
Gaskets are used as static (fixed) buffers between two flat surfaces. Some of the most common gasket materials are asbestos, copper, cork and rubber. Asbestos sheeting is used where heat-resistant gaskets are required. It is widely used for connections in exhaust systems. Most asbestos exhaust gaskets have a thin copper foil around the edges to prolong their service life.
A hard copper washer is used for spark plugs when a semi-soft but incompressible gasket is required. Seals can be used as oil seals between the engine crankcase and fittings, and where a seal is required, they can occupy irregular clearances or change due to surface roughness or expansion and contraction.
Rubber sheeting may be used where compression fittings are required. Do not use where it may come into contact with petrol or oil, because rubber is very quickly destroyed under the influence of these substances. The seals are used in hydraulic systems around cylinder heads, valves and other components. The seals commonly used for this purpose are in the form of an O-ring similar to an O-ring.
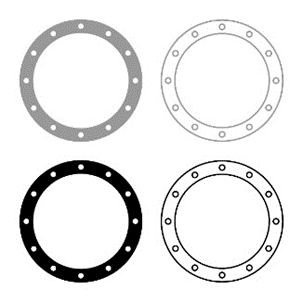
SEALING COMPOUNDS. HYLOMAR AEROGRADE
Certain areas of all aircraft are pressurised to resist atmospheric pressure, preventing fuel leaks, water vapour ingress or corrosion due to weather sealing. Most sealants consist of two or more ingredients, properly selected and mixed for best results. Some materials are ready to use out of the box, but others require mixing prior to application.
Hylomar Aerograde is a highly engineered, non-setting, non-hardening jointing compound for use in the aircraft industry with a wide operating temperature range of -50°C to +250°C. Hylomar Aerograde was developed in conjunction with Rolls Royce – Aerospace Division for sealing gaskets in turbine engines.
Hylomar Aerograde is resistant to:
Air, water and oils
Turbine and piston engine combustion products
Water/glycol and methanol/water mixtures
Petroleum and synthetic diester lubricating oils
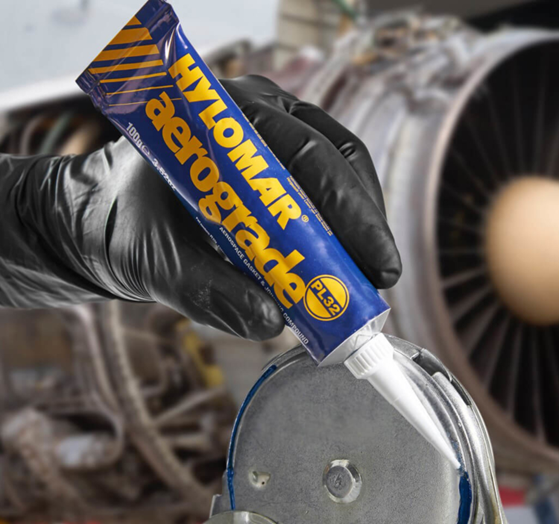
ONE PART SEALANTS
One-component sealants are prepared by the manufacturer for direct use. However, the consistency of some of these compounds can be modified to suit a particular application. If dilution is required, use the diluent recommended by the sealant manufacturer.
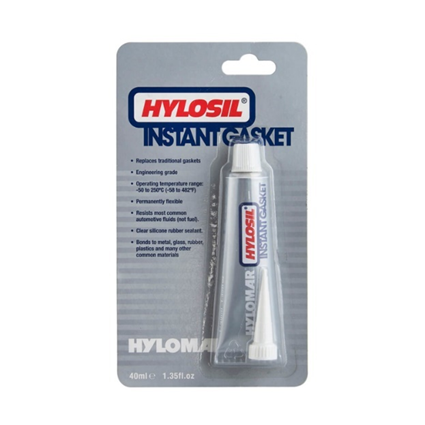
TWO COMPONENT SEALANTS
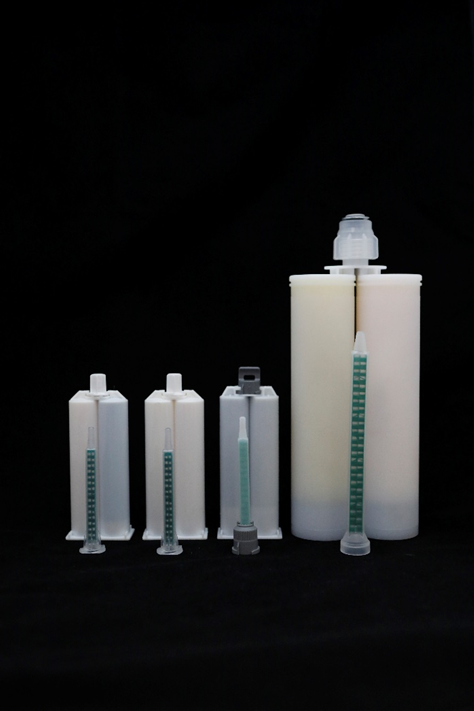
Two-component sealants are formulations that require separate packaging to prevent curing prior to application and are identified as base and accelerator sealants. Any change in the recommended proportions degrades the quality of the material. By mixing equal parts by weight of the base component and the catalyst, the two-component sealant is mixed.
All sealant material should be accurately weighed according to the sealant manufacturer’s recommendations. The sealant material is generally weighed using scales equipped with specially prepared scales for different amounts of sealant and accelerator.
Thoroughly mix the base sealant and accelerator before weighing the sealant. Do not use a dry, caked or flaking accelerator. Preweighed sealant kits do not require weighing the sealant and accelerator prior to mixing when thorough mixing is required. After determining the required amount of promoter and base sealer, add the promoter to the base sealer. Immediately after adding the accelerator, mix both parts thoroughly by stirring or mixing, depending on the consistency of the material. Stir the ingredients thoroughly so that no air enters the mixture. Mixing too fast or for too long will generate heat in the mixture and reduce the normal application time (working time) of the mixed sealant. To ensure that the mixture is well mixed, test by applying a small amount to a clean, flat metal or glass surface. If seeds or lumps are found, continue mixing. If spots or lumps cannot be removed, the shipment is rejected.
The pot life of mixed sealant is 1 ⁄2 to 4 hours (depending on sealant type); therefore, apply mixed sealant as soon as possible or keep in a cool place. The curing speed of mixed sealants is affected by variations in temperature and humidity. Sealant dries very slowly if the temperature drops below 60°F. 77°F at 50% relative humidity is ideal for curing most sealants.
The curing process can be accelerated by increasing the temperature, but in no case should it exceed 120°F at any time during the cure cycle. Heat can be applied by means of an infrared lamp or hot air. If hot air is used, it must be properly filtered to remove moisture and impurities. Do not apply heat to any surface adhesive installation until all work has been completed. All contact surfaces must have all fasteners, permanent or temporary, within the limits of the sealant application. Sealants must cure to a non-stick state before topcoating (non-stick consistency is the point at which a sheet of cellophane pressed against the sealant will no longer adhere).